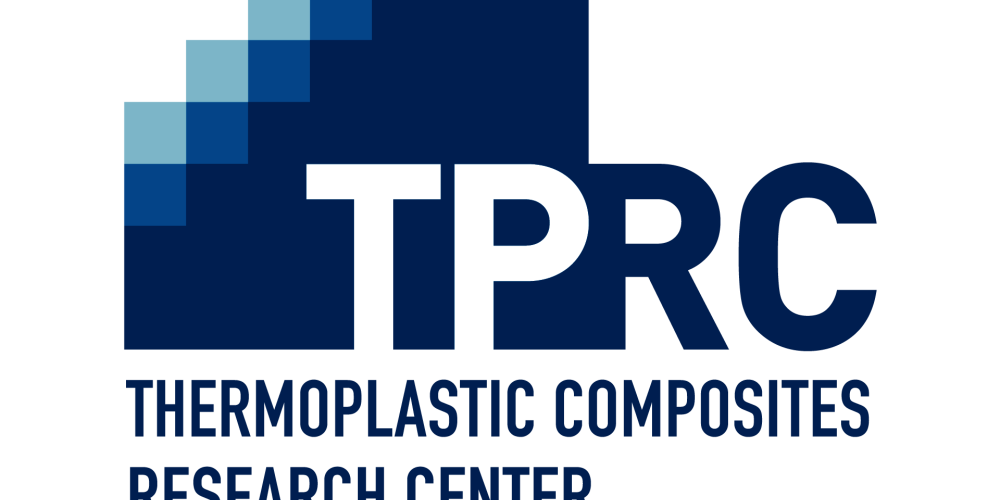
The SAMPE Benelux Spring meeting 2022 took place on May 18th at TPRC, the ThermoPlastic composites Research Center in Enschede. TPRC technical director Sebastiaan Wijskamp welcomed about 70 SAMPE guests and explained how TPRC grew from its birth in 2009 to a research group of about 45 researchers today. TPRC`s focus is on process-material interactions in thermoplastic composites (TPC). Today`s prime challenge is to make larger parts without defects, also complex and thick ones. Hence the theme of our meeting “Large Scale Manufacturing with Thermoplastic Composites”. TPRC researcher Erik Krämer explained first how tool/ply friction is the underlying cause of fiber waviness creation during TPC laminate consolidation. Alexei Vichniakov from Airbus presented a new hydrostatic press consolidation technology whereby large cylindrical structures that include stiffeners and frames can be moulded in a single step. In a following presentation, Peter Boer of DTC Collins Aerospace explained how his company uses an integrated approach to produce large, complex stiffened thermoplastic composite structures. To conclude the morning session, Bram Jongbloed showed the latest SAM|XL developments in ultrasonic welding, whereby clever design of the consolidator and sonotrode can increase the weld strength and reduce pores.
After a welcome lunch and networking break, the winners of the SAMPE Benelux student competition shortly introduced us to their research work. Arianna Tavano of KU Leuven showed us how biaxially oriented PP laminates can be used to make suitcases and Sofie Verstraete – also from KU Leuven – explained how short straw flax fibre stiffen a PLA matrix. During the last 2 presentations, Joachim de Kruijk explained NLR`s role in the STUNNING project wherein the largest thermoplastic aerospace part worldwide is moulded and Dany De Kock showed that JohnsManville will bring PA6-organosheet laminates to the market whereby the anionic polymerization of the PA6 allows to impregnate thick and dense fibre stacks, resulting in fast production of TPC with high fibre content, usable in automotive parts like battery elements.
To close the meeting, TPRC organized a networking drink in its labs, leaving the visitors the time to explore at ease the TPRC welding facilities, its Coriolis Automated Fibre Placement (AFP) machine, its fully equipped mechanical test lab with unique test setups to characterize the material-process interactions in TPC or the setups whereby TPRC validates the validaty of its forming simulations.